Looper control is widely used in modern rolling technology to realize automatic control of continuous rolling. Looper control can make use of looper scanning instrument of excess material between two adjacent frame scanning, through excess material arc curve height of rolled piece to measure the length of the loop, and then compare and contrast the loop height of the measured and already set loop height, automatically adjust the speed of the adjacent frame, in order to keep looping measured value and the consistency of the set value.
Looper control is applied to high speed rolling, which can effectively control the quality, yield and yield of products on the production line. It can be seen that looper control plays an important role in the whole high-speed wire production, so the accuracy of looper control must be ensured.
一、The concept of looper
Looper refers to the automatic control system to adjust the speed of the adjacent frame, so that the arc of excess material generated between the frame can be maintained dynamically. Looping by looping commonly sets, supporting roller, roller, pneumatic system (motor) and loop scanner in five sections, it plays a role of guidance and support of the supporting roller and a set of roller, loop scanner to measure the height of the loop, pneumatic system (motor) is responsible for controlling the roller set of ups and downs, as shown in figure 1.
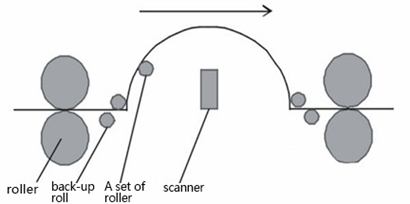
figure 1 Schematic diagram of looper structure
Looper plays a very important role in high speed wire tension-free rolling. The existence of looper solves the problem of pile pull in the rolling process. When the amount of material between adjacent racks is reduced, the looper adjusts the height of the sleeve to reduce the height of the sleeve, which plays a buffer role to prevent the material from stretching and affecting the accuracy of the material size. Because looper can make good use of the excess material between the racks, but also to prevent the emergence of stack steel phenomenon.
二、Looper control principle and way
2.1 Looper control principle
According to the requirements of related technology, looper control is adopted in the process of high-speed wire rolling in order to realize tension free rolling between each frame of pre-finishing rolling and between finishing rolling and middle rolling. It is necessary to set an appropriate height and adjust the rotation speed between adjacent racks with the height converted to compensate the main transmission speed difference and ensure the accuracy of wire products.
2.2 Looper control mode
Looper control is divided into the starting stage, the control stage and the stage. Looper height category is generally controlled in 0~500mm, looper scanner output signal between 0~ 10V. In the casing stage, the dynamic speed drop of the system is about 5% when the rated load is suddenly increased, and the recovery time is about 0.5~1s. In this process, when the frame bites the steel, it will affect the speed relationship between the frames which has been set, leading to the accumulation of rolled parts between the frames, resulting in excess rolled parts, which will form looper under the action of the sleeve roller. The artificial setting height value will affect the speed correction of downstream frame. In general, after the setting is stabilized, the artificial setting height value and the actual height value will fluctuate in a very small range. To precise control of sets of roller can be taken to adjust the roll up of time, judging by downstream frame bit steel signal, when the downstream frame bit steel, a set of roller is action, through the loop scanner to tracking control of rolled piece, rolled piece through the loop scanner, then to calculate the speed of the upper frame and loop scanner and frame between the distance, To calculate the time, through the time of the final adjustment of the time of the roll. After the setup is complete, the control stage is entered, during which the control system corrects the real-time speed of all racks through cascade control. To ensure that the gap between the specified height and the actual height of the looper is limited to a small value to achieve balance, the looper control uses a PI mediator to superimpose the output value on the given value of the upstream rack speed. As long as the value is within the range, the system determines that the looper height is appropriate and no adjustment is made to the speed.
Finally, the looper stage. At this stage, there are two ways to control the process flow: one is to control the looper by setting the distance in the system, but this way often causes the pile tail of the material, so it is usually not used; The second way is controlled by the biting signal of the upstream frame. When the tail of the rolled piece is separated from the upstream frame, the setting roller starts to lower to the bottom. In this process, it is necessary to adjust the speed of the upstream rack and reduce the height of the looper to prevent tail slashings.
三、Looper faults and troubleshooting methods
3.1 Looper lifting roller cannot rise and fall normally
There are many reasons for looper failure, mechanical, process, electrical problems on any one hand may lead to failure. When the hair life set set roller can not normally rise and fall, usually there are the following reasons:
◆ First of all, the looper scanner detection environment is abnormal, which means that the scanner lens may be contaminated, the detection port is not aligned, a large number of fog blocking materials affect the detection, or the bottom of the guide groove has oxide sheet;
◆ Secondly, looper scanners, hot metal detectors damaged, unable to detect materials;
◆ Again, the reversing valve is blocked, the mechanical mechanism is stuck or the air pressure is insufficient to lead to the normal work of the sleeve roll.
3.2 The looper head is too high and the looper quantity is unstable
The looper head is usually too high because the impact speed drop compensation is too small, or the pressure down caused by a large bite Angle. The looper sleeve quantity is unstable, then by many reasons. Internal failure of looper scanner results in irregular fluctuation of looper quantity. Looper table design is not reasonable or improper mechanical adjustment, set of fluctuation in the formation of looper after the beginning, amplitude will change along the law of the material, so it can be adjusted by adjusting the position of the supporting roller and the next set of roller. The loop instability can also be caused by improper adjustment of the proportional control gain of the looper. Improper adjustment can cause the looper to be unstable, and the frequency of the looper will fluctuate evenly throughout the material passing. In addition, improper installation of guide will also lead to the looper sleeve amount of instability, material in the roller gap constantly swing, resulting in changes in the deformation of the frame, so that the looper sleeve in rolling frequency and amplitude become uniform.
3.3 Tail flap when looper falls
In the last step, the looper falls at a given slope distance that is too long, resulting in a delay in falling, which directly causes the looper to throw its tail. When the material size of the front frame is seriously out of tolerance and excessive wear, and the corresponding rolling guide opening is too large, the material will lead to tail-shedding stall of the living sleeve, and finally appear tail-throwing.