Bridge-type grab ship unloader is cutting edge special high-altitude bulk terminal equipment, the driver cab switching operations, there are large blind spots, the current bulk terminal bridge-type grab ship unloader cart driving mechanism is still using mechanical travel switch as an adjacent equipment collision detection and protection, can only detect the collision of ship unloader, adjacent The effective distance between the ship unloader and vehicles and pedestrians cannot be detected, which leads to frequent collisions between the ship unloader and vehicles or pedestrians, affecting the equipment and production safety, and causing direct and indirect economic losses to the company's production. Therefore, it is urgent to find a reliable, accurate, all-weather uninterrupted monitoring auxiliary equipment to assist the driver to move the operation, reduce the accident collision rate, so as to reduce the accident shutdown, to achieve efficient and safe production.
◆ Principle of laser ranging
Laser ranging adopts time of flight (TOF) method, that is, the laser shoots a small beam of laser to the object mark, and the reflected laser is received by the photoelectric element. The built-in timer measures the round-trip time T of laser beam, and calculates the object mark position S: 2S = c* δ t, S = C * δ T /2, (electromagnetic wave propagation velocity C = 3* m/ S, δ t = T2-T1, T2 is the return time of electromagnetic wave, T1 is the emission time of electromagnetic wave)
◆ Application of laser ranging technology in ship unloading machine
The bridge grab ship unloader laser rangefinder anti-collision system includes laser rangefinder, data transmission link, PLC of ship unloader, variable frequency drive system of ship unloader and early warning device. Laser range finder by fixed bracket installed on the ship unloader landside leg left and right door, laser range finder by data transmission link connected to the ship unloader PLC communication, ship unloader PLC were described and warning device, ship unloader cart variable frequency drive system, the communication by laser rangefinder monitoring ship unloader landside legs around the left and right door close to the signal, The approach signal is fed back to PLC of ship unloader through data transmission link. PLC of ship unloader controls the frequency conversion drive system of ship unloader to slow down or stop, and PLC of ship unloader controls the early warning device to send out early warning signal. The distance measurement system can effectively prevent collision with ship unloader, vehicles, or pedestrians, reduce safety risks.
◆ Installation method
Through the fixed bracket installed on the ship unloader landside leg left and right door, laser range finder by data transmission link connected to the ship unloader PLC communication, described in the ship unloader PLC respectively and warning device, ship unloader cart variable frequency drive system, the communication by laser rangefinder monitoring ship unloader landside legs around the left and right door close to the signal, the process of switching operation, The adjacent ship unloader slows down within 3 meters, and stops the operation of the truck after approaching 1 meters; And it can realize automatic deceleration or stop when approaching other obstacles; Early warning devices (buzzer alarm and warning light) should be installed in the driver's cab to remind the driver to pay attention to driving safety, so as to take timely and effective measures to avoid collision.
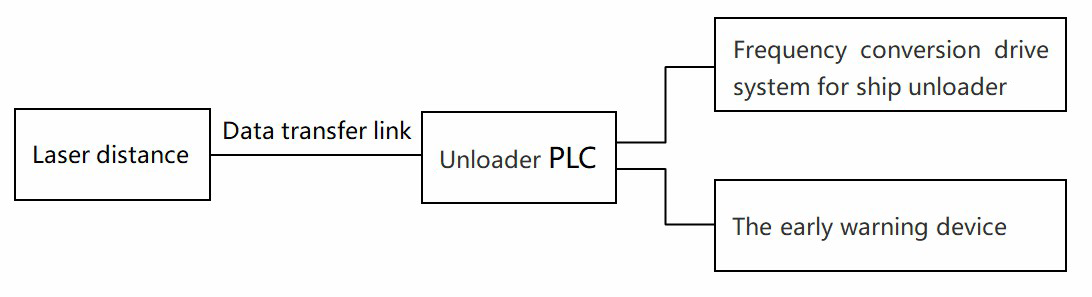
Ship unloader cart ranging collision system connected to the laser range finder, when the driver operating ship unloader switching operation, a laser range finder to detect the ship unloader, equipment, vehicles or pedestrians distance is relatively close, feedback signal into the ship unloader PLC immediately, send out alarm in the cab warning device, remind operators make appropriate operation in time, At the same time, THE SHIP unloader PLC controls the frequency conversion drive system of the ship unloader to decelerate or stop, which effectively avoids the collision between the ship unloader and the adjacent ship unloader, equipment, vehicles or pedestrians, and reduces the potential safety hazard.